Understanding Closed Loop Cooling Water Systems
A closed loop cooling system consists of four elements:
- Heat Load - Industrial process or equipment that reduces heat as a by-product; for example, an air compressor or furnace.
- Heat Exchanger - Device to transfer heat energy to a cooler medium; for example, a fluid cooler or radiator.
- Pump System and Controls - Recirculate heat transfer fluid from heat load to heat exchanger.
- Piping System - Pipe and valves used to connect the system components; permits fluid circulation between heat load, heat exchanger, and pump system.
The pump / control system circulates a heat transfer fluid through the piping system to heat exchanger to capture the heat produced by the heat load. The heat is dissipated by one of several possible cooling methods, i.e., ambient air cooling, evaporative cooling, or refrigeration.
Calculating Heat Load
To design an industrial cooling system, the heat load must be determined. Total heat load is expressed in BTU, or British Thermal Units per Hour.
British Thermal unit (BTU) - Energy required to raise the temperature of one pound of water one degree Fahrenheit.
Total Heat Load can be calculated by using the following heat transfer formula:
BTUH = 500 X Temperature Rise X Flow
500 - Weight of one gallon of water x 60 minutes.
Flow - The flow of coolant through the heat load expressed in gallons per minute (GPM).
Temperature Rise - The difference between the entering and leaving coolant temperature.
This formula is valid for water as a coolant. For any other liquid, correct with the specific heat and gravity.
Thermal Precision considers several factors when designing an industrial cooling system:
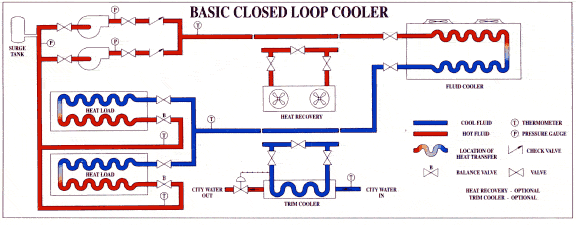
- Maximum inlet temperature to heat load
- Ambient air conditions and elevation
- Water quality and availability
- Environmental conditions